What is PLC?
PLC full name is Programmable Logic Controller, it is a designed for industrial automation and control systems,as we can it is an electronic products, but with smart system and can be programme. It operates as a digital computer used to control automtion moving action and processes, such as assembly lines, prodction line,robotic devices, or any activity that requires high reliability, ease of programming, and process fault diagnosis.
PLC is the most popular electrical products and system in nowadays automation industry.PLC is designed to withstand harsh industrial environments including extreme high or lower temperatures surroundings, vibration, and electrical noise. They can control a wide array of machinery and processes through digital and analog inputs and outputs. Programmable in various languages, including ladder logic, which visually resembles electrical relay schematics, PLCs are essential in modern manufacturing and production industries to enhance efficiency, precision, and reliability.Unitl 2024, it is still one of the best choice for automation equipment.
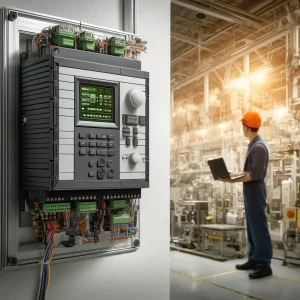
Popular PLC Electrical Control Cabinet Structure
The PLC electrical control cabinet, for different fucntion ,model and size , its with different design. It is machine Brain which adaptable to a variety of industrial automation control applications, regardless of their size. The structure of the PLC control cabinet is compact, operates stably, water proof and offers comprehensive functionality. It can be customized according to the actual control scale, allowing for either single-cabinet automatic control or multiple cabinets interconnected via an industrial Ethernet or fieldbus network to form a Distributed Control System (DCS). The PLC control cabinet is well-suited for diverse industrial automation control scenarios of any scale.
The PLC electrical control cabinet consists of air switches, power supplies, PLCs, relays, terminal blocks, bus ducts, signal isolators, distribution devices, safety barriers, and other equipment. Here’s a detailed overview:
- Electrical Components: Components such as switches, circuit breakers, contactors, and motor protection devices are selected with redundancy in capacity and model specifications to ensure reliable operation of the electrical system.
- Power Management: The control cabinet includes a main power circuit breaker. Each load and control power source has its own circuit breaker. Power input and output lines are connected to terminal blocks, and the cabinet contains both neutral and ground busbars.
- Cable Management: Connection cables between primary equipment should use national standard conductors, neatly bundled and laid in cable trays.
- Wiring Identification: Connections should be differentiated by color and numbered for easy identification.
- Cabinet Color: The cabinet is painted in a light yellow-gray color (82 Y13), as specified by the National Coatings and Color Standardization Technical Committee’s “Paint Film Color Standard Color Card” GSB05-1426-2001, and the color is consistent both inside and out.
- Sealing and Protection: The control cabinet is designed to meet the IP65 protection rating, ensuring it is dust-tight and protected against low-pressure water jets from any direction.
This design ensures that the PLC control cabinet can meet stringent safety and operational standards, making it suitable for diverse industrial applications.
Control system of an automatic liquid filling machine
The PLC is the core of the control system. It is programmed to manage the sequence of operations in the filling process. This includes controlling the start and stop of the pump, the opening and closing of valves, the timing of each fill, and the movement of containers through the machine.Most of the packaging equipments are adapt PLC control system
HMI (Human-Machine Interface)
The HMI is a user interface that allows operators to interact with the machine. It provides visual feedback about the process, such as current operations, errors, and system status, and allows for adjustments and manual control when necessary